RCF Precision Transducers
Rechercher des produits RCF
Choisissez le système de recherche
Rechercher un produit
Les innovateur des haut-parleurs
RCF boasts over 75 years of experience in designing and manufacturing transducers, with a particular focus on moving coil loudspeakers. Our transducers are engineered to optimize the balance between power delivery and sound purity, achieving minimal distortion and the capacity to endure high power levels for extended periods.
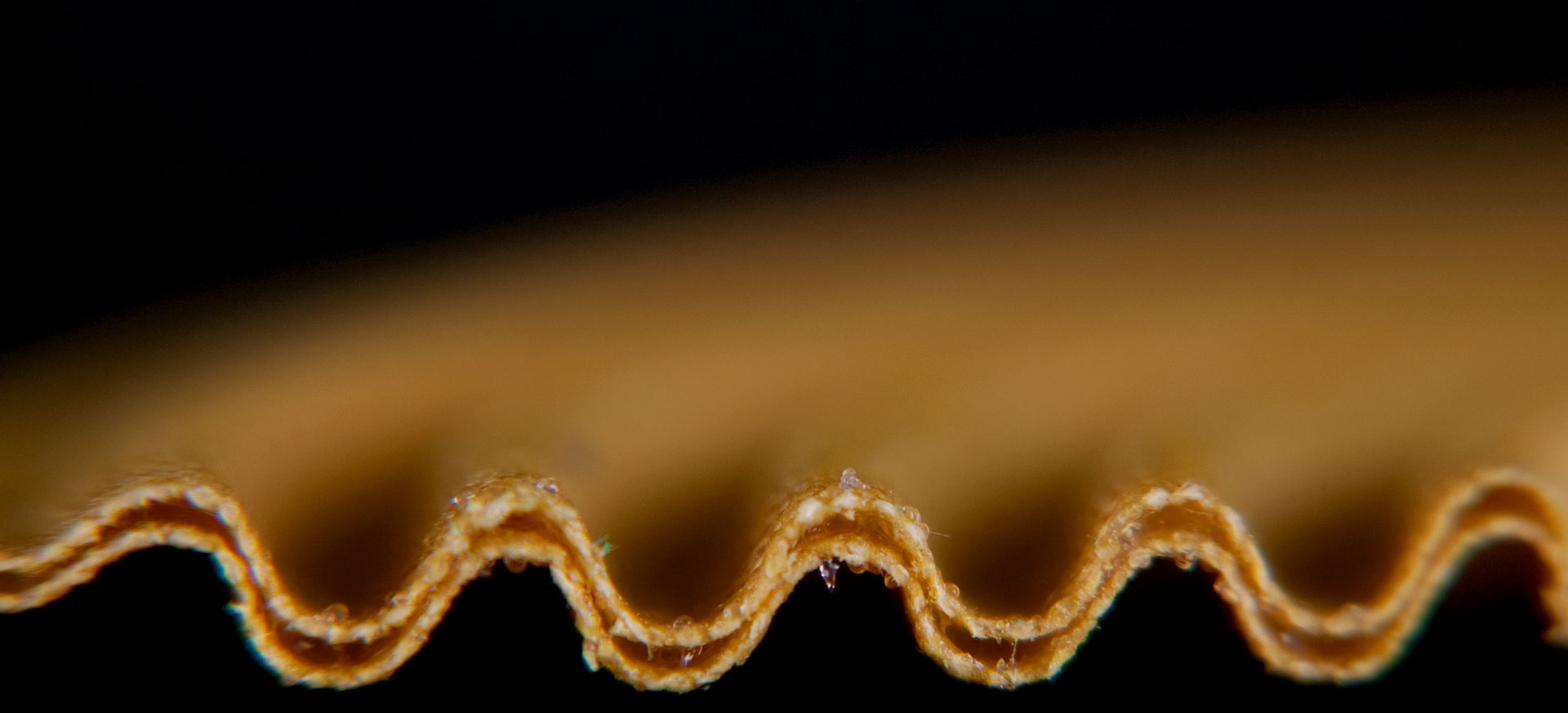
High-Grade Materials
The inclusion of a high-damping cellulose cone, double polycotton-polyurethane spiders for outstanding stability and control over the moving mass, and a substantial heavy-gauge treated triple cloth surround, contribute to the moving mass's exceptional strength and excursion control. Additionally, a water-repellent treatment ensures suitability across various environments.
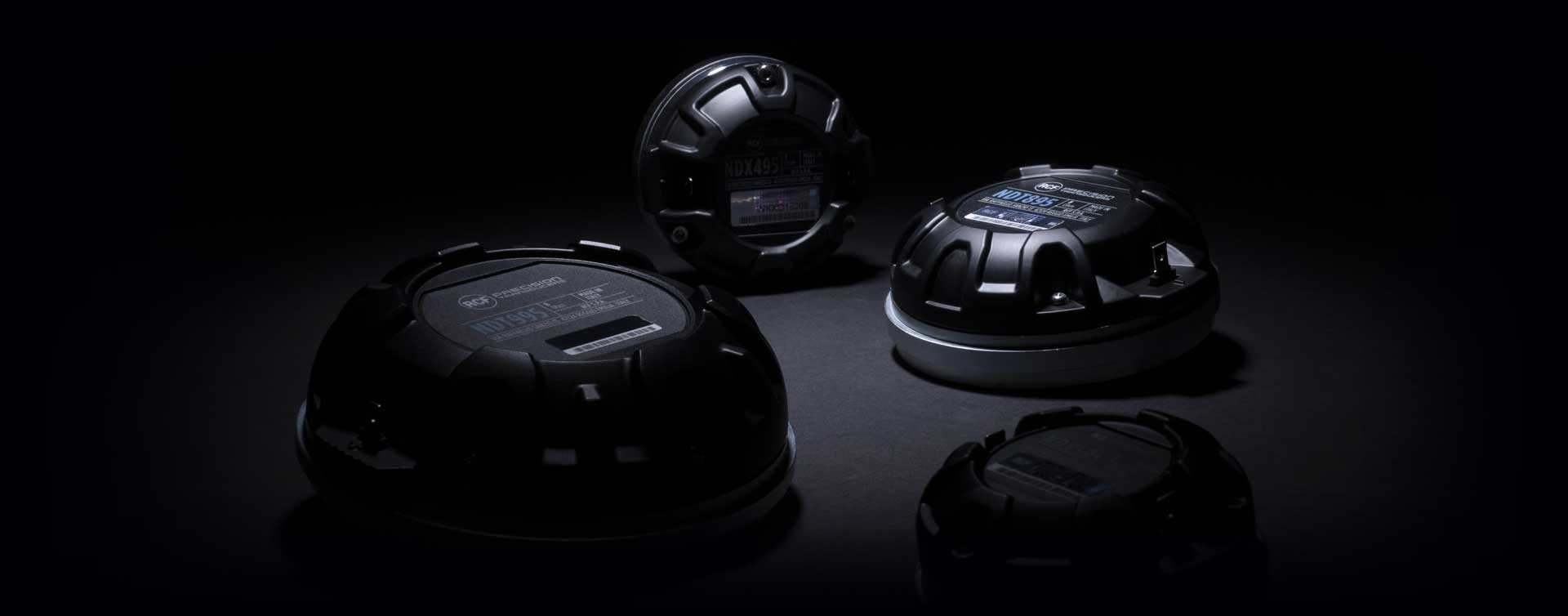
Advanced Compression Drivers
High Power Magnet Designs
Magnet geometry and configuration are optimized for maximum flux density, incorporating thermal management to ensure reliability. Techniques such as computer-aided magnet optimization and FEM analysis refine magnet weight, flux density, and field saturation, significantly reducing driver weight and harmonic distortion.
The T-pole design minimizes flux modulation in the magnetic assembly during typical voice coil movements within the gap. We developed specially designed rings in copper for compression drivers and aluminum for cone transducers. Pressed onto the pole piece, the ring modifies and reduces the magnetic circuit and voice coil inductance, enabling a controlled extension of the acoustic frequency response.
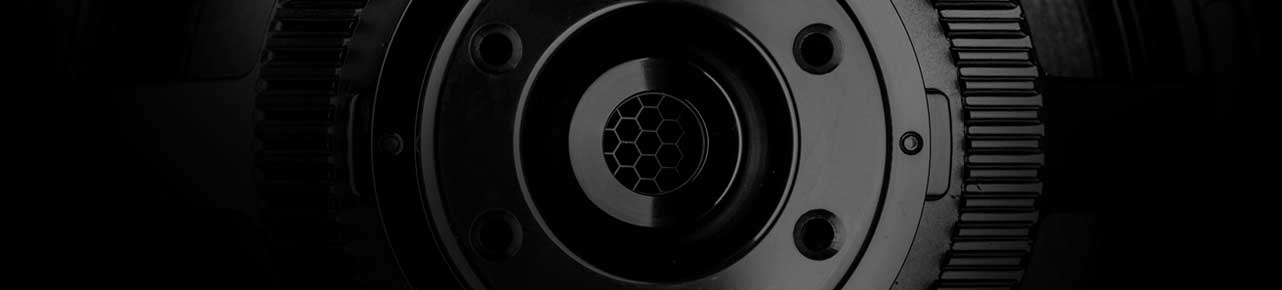
Dual Forced Hyperventing System
Hypervented cooling designs combine various components to create an ideal ventilation system. The RCF engineering team emphasizes finned cooling channels and optimizes the surface area of the front magnetic plate for efficient heat dissipation. The double silicone sealed spider design functions as an air pump, expelling hot air and drawing in fresh air with each movement of the cone assembly.
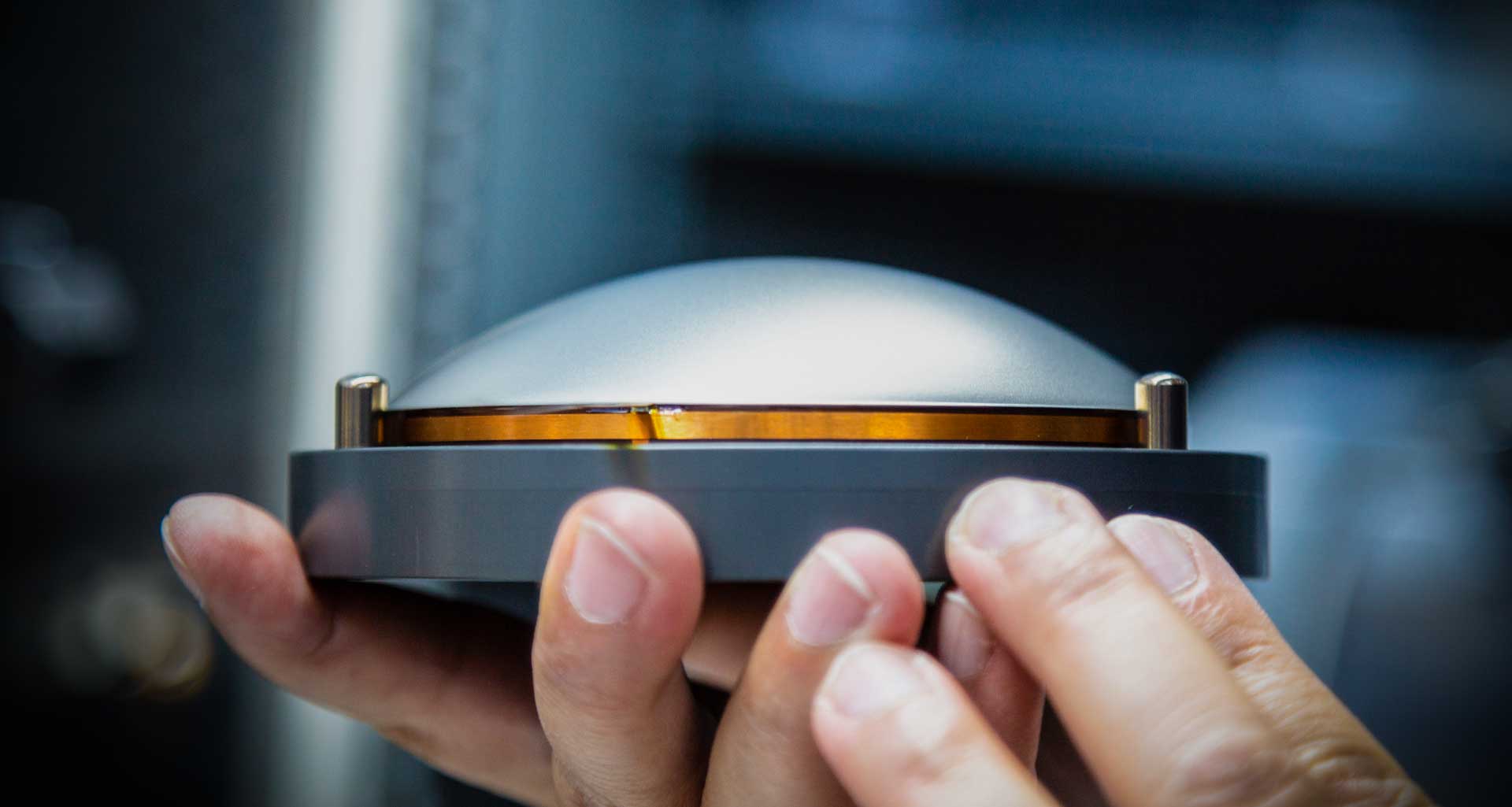
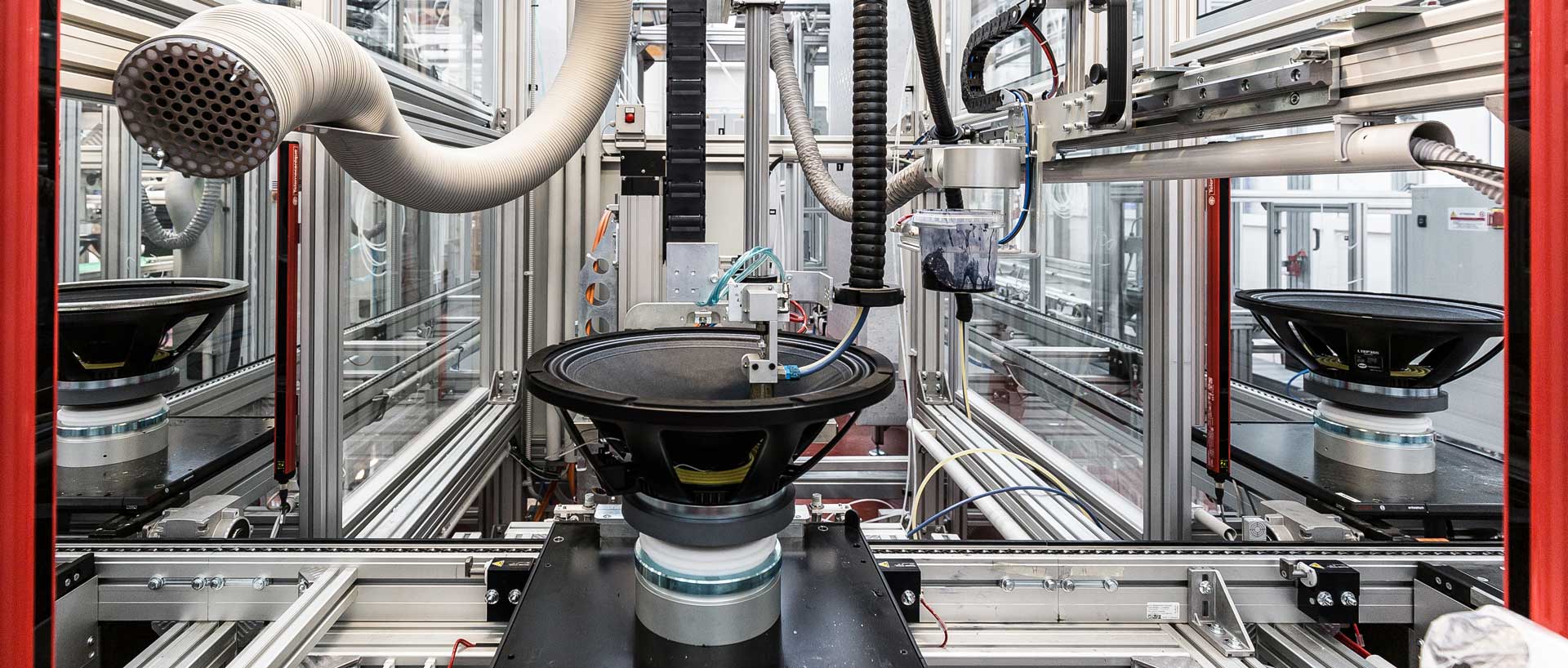